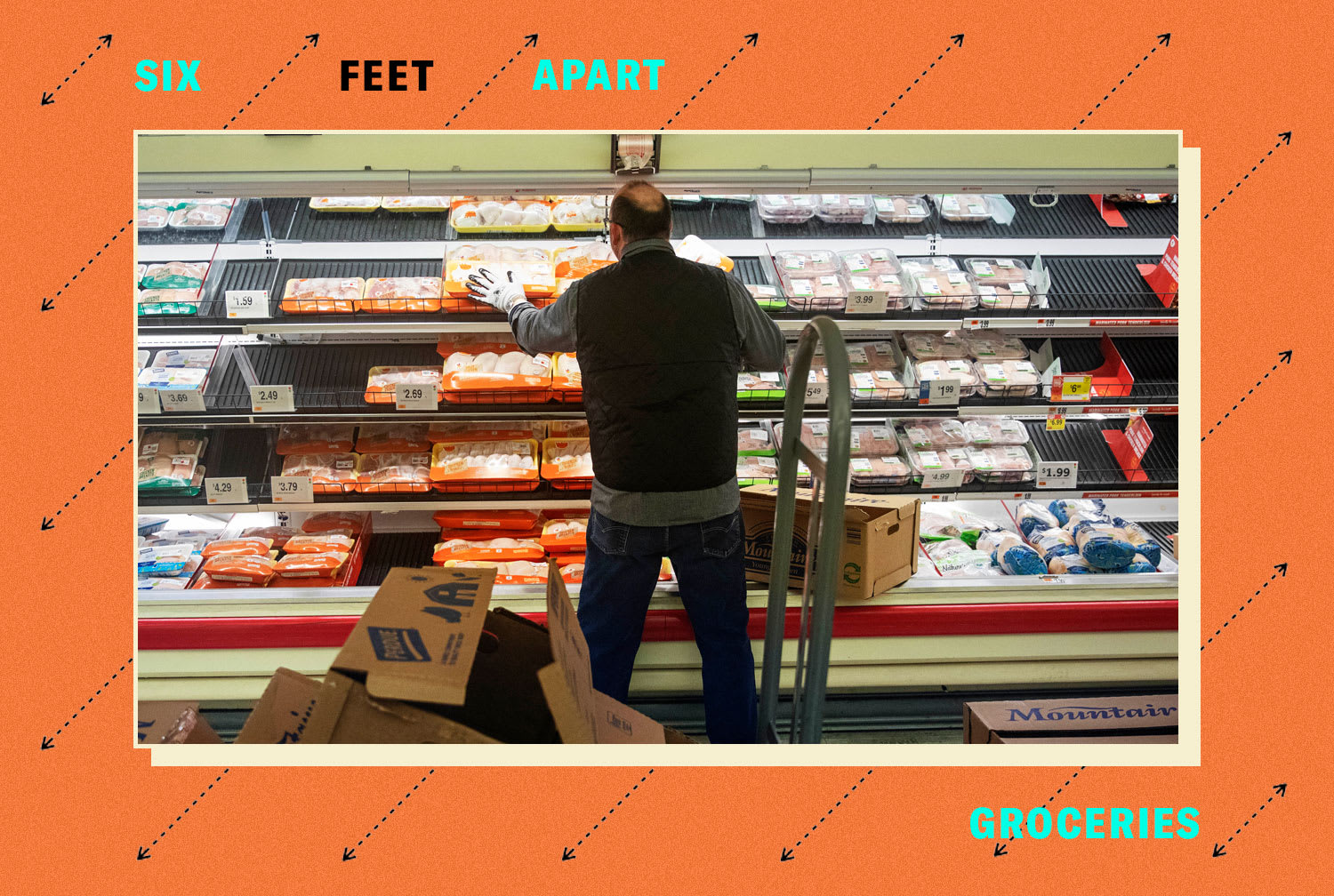
In This Episode
In the first episode, Alex talks to two essential workers about what it takes to bring you your groceries in the middle of a global pandemic. Jeff Dunn is the CEO of Bolthouse Farms. He’s had to come up with big, bold solutions to keep his hundreds of employees safe all while still getting us our carrots without delay. Tony is a Trader Joe’s crew member trying to balance customer and company needs with his own safety. As Americans everywhere deal with the challenge of putting food on the table—literally—Alex explores the unprecedented sacrifices and unheard-of arrangements required to keep us fed in a time of crisis.
Transcript
Alex Wagner: Hi and welcome to Six Feet Apart. I’m Alex Wagner, journalist and co-host of The Circus on Showtime. In this series, we’re talking to the men and women making tough, complicated decisions in the face of our global pandemic, and the people whose jobs and lives are directly affected by those Hail Marys. Today, we’re looking at the food chain, specifically groceries. Now that we are a nation of home cooks, Americans, myself included, have become real reliant on the supermarket for basic survival. Without a constant replenishing of the shelves, we would be completely lost, literally. Hummus, baby carrots, Eggo waffles—it’s all we got. Never before has the availability of canned black olives held such sway over our collective psychological well-being. I cannot express to you the sense of cosmic victory at my house when the local market finally restocked creamy peanut butter. As the supermarket goes, so goes the nation. But the companies that get those foods to the shelves aren’t immune to the virus. Nor are the people working in the supermarkets, the men and women we buy our groceries from. How do you manage a national food supply chain, one that is dependent on people to grow, harvest, package, and distribute that food in the middle of a global pandemic? Are we headed toward a national food shortage? Are we going to make it through this thing with our elbow macaronis intact? And what does it feel like all of a sudden to be thrust onto the front lines of a crisis where the job of supermarket clerk has now suddenly taken on crazy importance and very real risk? That is what we’re going to find out about today, the great grocery war against COVID-19. First, we’re going to talk to Jeff Dunn, the CEO of Bolthouse Farms. That’s a 100-year old vegetable company that is the country’s largest supplier of baby carrots. You didn’t realize how much you needed those baby carrots until you had to contemplate a reality where you might not have them. Am I right? Then we’ll hear from Tony, a crew member at a Trader Joe’s location on the East Coast. Trader Joe’s has been in the news this week. Right after we spoke to Tony, BuzzFeed reported that more than half a dozen employees at least four stores have tested positive for coronavirus. But those Trader Joe’s locations didn’t close. Managers didn’t advise employees about the positive test results, nor did they perform enhanced cleaning afterwards. Tony agreed to speak with us, but he requested that we not use his full name. And just to be clear, his opinions are his own. Also, you may notice some audio hiccups throughout these interviews, and that is because we are just trying to make it work in the middle of a pandemic. Apologies.
Alex Wagner: Let’s just start at sort of the beginning for people who aren’t familiar with Bolthouse Farms, can you give me a sense of the scale of what you guys do?
Jeff Dunn: Yeah, well, thanks for having me on, Alex. Bolthouse Farms, we’re a large, you know, vegetable grower: carrots. So we grow about 40% of the carrots, fresh carrots in North America. So that’s over a billion pounds of carrots to give you an idea. Most of those are grown in California, but we have farms in eastern Washington and eastern Canada and in Georgia and now in Arizona. So, you know, we grow them all over the country regionally. But the big, you know, produce growing and processing is in California. So that’s the agricultural side of our business. We also have a large juice business, both of which have, you know, spiked up dramatically here in the face of COVID and what’s going on in the country.
Alex Wagner: Because you guys are so, I mean, 40% of the carrots we consume in the country is a daunting a huge number of carrots. Can you just walk me through the life of a carrot, a baby carrot?
Jeff Dunn: Well, you bet. So, you know, look, seed to, you know, to a carrot coming out of the ground is about 140 to 160 days in the ground growing. Takes about three months before that to prepare the soil. So that carrot, you know, you’re getting in the grocery store took about nine months from start to finish. For baby carrots or other cuts of carrots, we’ve got a highly-automated process for those carrots are washed, peeled, cut into two inch kind of plugs, and then those are peeled down to be that baby carrot you see in the store. And to give you an idea what’s happened in the past four weeks, orders we got from customers started spiking up about three or four weeks ago, and then last week we probably had 400% the orders that we could normally ship in a week. But the 400% growth is nothing compared to what I’ve seen in toilet paper and paper towels, which are showing 1000% growth. And I think people are working really hard to catch up but it’s a, it’s kind of unprecedented in its effect.
Alex Wagner: At what point in the news cycle here about coronavirus, about COVID-19 did you realize you were going to have a problem on your hands?
Jeff Dunn: Well, we realized it back in January when China hit because we source a lot of packaging, things like that in China, as well as some ingredients for our beverage business. About four weeks ago, we kind of went into full crisis management mode in terms of taking all the actions in our facilities. You know, we probably had an early warning, and look, in business, you can hope for the best and there’s a lot of that going on, but you have to plan for the worst and that’s what we’ve been doing. And as a result, we’ve been able to stay ahead of this in terms of, you know, really two goals for our company. One is the health and safety of our employees and two is business continuity because we have to feed people. But we don’t see that as a trade off. We can’t operate without our people so if we don’t keep them safe, we don’t have a business. All of a sudden, people certainly appreciate labor in a way they didn’t before because machines are great, but they don’t do everything and people have to run the machines. And so I think the kind of second wave heroes here beyond the health care industry who is just, you know, saints, in my opinion, are the people who are keeping everyone fed, because the only thing that would make the situation worse is no food.
Alex Wagner: You kind of, in this moment Jeff, you have two problems and neither one of them are very good. One is this giant 400% surge in demand, coupled with a pandemic that is laying waste to the nation’s health care system and that has a terrifyingly high fatality rate and is, continues to spread. We’re not at the peak, right? So did you guys have a plan for something like a pandemic? I mean, is that something the food industry has, like, thinks about, or were you just kind of going with this on the fly?
Jeff Dunn: Well, we did have, not a pandemic response, but we had an emergency response. So we had those plans. You know, we have 1,700 people who work at our plant, but a lot of those are in packaging and warehousing and distribution. We, in order to keep the plant up and running literally over the past two weeks, one, we’re checking everyone into the plant, we’re taking their temperature. We also put all new sick policies and those kinds of things in place. We’ve also, by the way, been providing food and water for our employees because they can’t get it to the grocery store to take home. So all kinds of things to kind of be self-contained. And then, you know, the heart of this is we broke the plant of 1,700 people into teams of 10. They have their own break rooms, their own paths in and out of the plant, we sanitize behind them. So we reengineered how the plant runs in order to put social distance between the people actually working in the plant. You’ve seen with Amazon and others a lot of stress in especially warehouses, people working very closely to each other, not sanitizing things like forklifts after they use them, and so we thought all the way through that, and because we’re a food business, what we’ve drawn on is really our food safety crisis management. So if you had a pathogen or you had a food safety incident, these are all the things you have to do anyway in the plant. So for us, we were very well prepared. We have an incredibly experienced team in this. But even with that, we’ve been 24/7 for four weeks now and I don’t think we slept more than two or three hours a night. I mean, it’s because think about reengineering how you do things at that level. It just, you don’t snap your fingers. It requires coordinating a huge amount, including organizational communication. And our workforce is about 80% Hispanic, Spanish is your primary language. So that makes it just a little bit, you know, more intense in terms of communicating.
Alex Wagner: So you’ve broken up your warehouse into pods of 10 effectively, and can you just explain that this sort of logic behind that? You want to keep folks away from, you know, sort of large gatherings, right, but is it, is it also I mean, sort of a preemptive measure? For example, if someone on that team get sick, then you get quarantine 10 people and not 20 or 50 or 100. Is that the sort of logic there?
Jeff Dunn: Yeah. Yeah. And so that’s exactly right, Alex. So by breaking into the groups of 10, you do a couple of things, one is you limit the cross contamination, obviously, because not only are they working in their sections, we took big sheets of plastic and created like walkways into their work zone and back out. So from the time they come in the plant, they’re going through this tunnel-like thing to their work zone. And their work zone, because there are groups of 10, we’re taking temperatures coming in. If you have a temperature we don’t let you come to work, we send it directly to get a test. If you come in and we find out post- you coming to work that you got sick, we now have necked you down just to those 10 people you worked with so we can then put them in quarantine. But this is very much guerrilla warfare. If you can break into small independent cells, they’re very hard to take them all out, if you, you know, spread them out through the plant. And so a combination of testing, constant communication, because our employees really want to know what’s going on, they very much appreciate that we’re trying to protect them and explain to them why we’re doing what we’re doing, and then identifying down to 10. And we have yet to have a positive COVID hit in the plant. We’re testing a number of employees right now, but we’ve now got a tracker. So if we get a hit, they can then, and we give that information to the CDC, they can start backtracking that person. And one of the things I think big problems here because we lost containment early as a country is you couldn’t track this thing, so now it’s so uncertain for exactly that reason. So we didn’t want the plant to replicate the experience the country is having right now, because statistically they’re going to get it. Like this is the problem, hoping for the best. It doesn’t work. You’ve got to run the math. You got to use things like science and mathematics and say, you know, if this stuff happens and half the people in California are affected, this plant’s going down if I don’t keep people on the line. So the first step is keep them healthy. The second step is if they get sick, move them out quickly. The third step is replace them seamlessly. And that’s how everything should be working. And look, Alex I want to scare the bejesus out of you, what would we be doing right now if this stuff lived on plastic or paperboard for two weeks?
Alex Wagner: Right. Yeah, no one wants to think about that. But is it your sense that other food producers, other growers are able to implement such a, you know, the same battle strategy? You talk about this like guerrilla warfare. Does everybody look at it like that?
Jeff Dunn: No. In fact, you know, depending on where you are in the country, you know, some people are just business as usual. Some are trying to, you know, much like probably Trump’s doing with the country is trying to balance this economic and, you know, health goals, and I think it’s a false dichotomy. I don’t think you can protect the economy if you don’t protect people, because this thing is just going to continue to spin. If this was a different situation where, you know, you had a much more intense, like infection rate relative to things like packaging, there is no game plan. So I was really surprised the Department of Agriculture, CDC and others didn’t have protocols down for infections and plants. I mean, they literally asked us three weeks ago, well, what do you guys think? And we’re like, what do we think!? What do you think? You know, we’re like, we’re just going to pull it out of our playbook and go, go, you know, as if it’s a food safety incident. And we just have really creative, smart people and we figured it out, but literally the playbook we ran should be a playbook that should be pulled out on day one. You should have gone to ten people day one. You should have done testing day one. From my standpoint, I’d love to never go through this again, but I think this is climate change and this is on us forever, and whether it’s a hurricane or a pandemic, our ability to respond needs to be massively upgraded. And that’s what we’re learning right now, I think more than anything.
Alex Wagner: When you split people up into pods, you have them walking through these plastic kind of tunnels to their workspaces, there is the looming threat of death, you know, in the news cycle and, you know, at water coolers everywhere. The nation is grappling with the sort of psychological toll of this moment of uncertainty. What is morale like inside your plants as workers have seen their entire sort of way of life changed professionally?
Jeff Dunn: I you know, it really makes me want to cry. I mean, these people step up like you can’t believe it. They weren’t afraid of coming to work. They wanted to know what was going on. But we took some actions early that I think supported this. One, we were honest. Two, we took all the high risk folks. We had some folks in their 60s in the plant, we sent them all home. We very quickly, you know, two weeks, more than two weeks ago, we went to work from home. We put a new sick policy in so people weren’t penalized for calling in sick. We didn’t want them to come in sick. And we’ve been pounding communication. The result of all that is that people trusted that we were trying to protect them and that we had this big surge of demand, they wanted the work. I think the other thing that has actually given them confidence is we started taking temperatures. We started, you know, communicating with them what we found. And not because I’ve said I’m not laying anybody off, I’m actually hiring people. There’s no risk of anyone losing their job here. And we’ve said to everyone, look, if you’re very concerned about this, talk to your manager. We’re willing to work with you. We don’t want anyone to take on something that they feel like it’s an undue risk. And again, people have stepped up in an incredible way. But I think if you don’t do it—Mark Cuban wrote a piece you may have seen, he said: brands will be judged by how they treated their employees during this crisis. And I think you see it already. You’re seeing some real fractures around companies that aren’t doing the right thing to protect your people. And I think it’ll be binary. I think you’ll be seen as doing it and being proactive, or lagging and just letting it kind of play out. And I think the latter is a disaster in your system.
Alex Wagner: The system that you guys have put in place gives me confidence about baby carrots and juices, but it doesn’t give me confidence about the sort of grocery world in general, because it really just doesn’t sound like everybody is doing what you’re doing, and nor can they on some level in terms of resources. And I guess I just worry. I mean, are we headed towards, I mean, we’re not at a food shortage right now, and I think it bears mentioning that repeatedly. But could that be a possibility in our near future?
Jeff Dunn: We have and, look, I’ve been dealing with it for 35 years, we have an incredibly strong food supply chain in North America. It’s not just the U.S., it’s Canada as well and some extent, Mexico. These are the strongest food supply chains in the world. You could see some individual commodities because of the high labor nature of them not get planted or not get harvested. So you could have shortages of individual things, but broadly stated, because it’s deep and there are really good kind of practices out there in terms of food safety that really came out in the last ten years with the Obama administration. I do think that it will beg some questions about, you know, the next time and what that means to us. Because, again, what’s keeping me up at night is not the way responding today. I think we’re going to be all right this time. It’s if it’s worse and more pervasive pandemic that impacts things like packaging, I don’t think anybody’s ever eve thought about. I’ve never read a paper on it. You know, you’ve seen the Bill Gates things about what, how to do with the pandemic. But a pandemic plus food riots is, you know, very problematic.
Alex Wagner: Yeah, that’s problematic with a capital P.
Jeff Dunn: I just don’t think we’re doing a particularly good job. I think individuals and certain groups are doing a good job and others are creating a false dichotomy relative to, well, economic development is just as important as people’s lives. And quite frankly, that false dichotomy is very dangerous because it’s going to kill people. So I hopefully a little more practical, non-gaslighting conversation takes place about what we as a people got to do to protect our children, our grandchildren. Enough of this shit already.
Alex Wagner: Well, you know, what’s good for staying healthy: carrots.
Jeff Dunn: Carrots, baby! Beta carotene and affordable, so everybody can enjoy it, not just the rich people.
Alex Wagner: You just got a 500$ surge in orders Jeff, congrats. Thanks as always. Jeff Dunn for your time, and wow, everything you’re doing behind the scenes to make sure we got those carrots and those baby carrots and those juices in our fridges. The country thanks you for your service, man.
Jeff Dunn: Well, same to you, Alex. Just keep challenging the bullshit, all right? Because it wears on everybody.
Alex Wagner: Tony, thank you for joining us in your off hours, when you’re not working at the store, you’re a Trader Joe’s crew member. Can you tell us what your responsibilities are in the store at Trader Joe’s?
Tony: A lot of people, when I tell them I work Trader Joe’s, I’m like, oh, do you work the register, or what do you do? I’m like, we do everything. That includes register working. You’re taking people out on the register, obviously bagging groceries, stocking in any of the sections that we have, like bread or produce or the dairy box or something like that. Also includes in each shift, you have an hour where it’s called helming, where you just generally wander around the store talking to customers, say, hey, can I grab you anything, how you doing, you finding everything all right? So it’s it’s an equal parts product and customer-oriented work, a whole slew of different activities within each of those.
Alex Wagner: So when did you first hear about the coronavirus?
Tony: I remember hearing about it, actually, I, I remember hearing about this as far back as February, maybe even into January, because I’m a very, very religious NPR Morning Edition listener. So they keep me up to speed on a whole bunch of stuff.
Alex Wagner: Did you ever think that you would somehow end up being on the front lines of the virus?
Tony: Very much, no. No, not at all to be honest. I thought I was being pretty practical in my concern to be like, is there a specific cause? Like, is this posing a direct threat to me and my lifestyle and everything sort of turned up, no. And my mom’s a physician and I was like, Mom, what’s your—classic turn to my mom in an hour of need—I’m like, should I be scared? She’s just like, no, you’re, you’re good to go, don’t worry, you’re not—. So at the beginning, I was very, took it very calmly. I was not really too worried, much as I think a lot of the country was. So it was a little shocking how, to the extent to which it has become a problem, for sure.
Alex Wagner: When did people at work start talking about the virus? When did you feel like, oh, this might be something I’m going to have to deal with?
Tony: So it was a day that I wasn’t working. It was the Thursday of that week when it became officially a pandemic, because I remember I was, the Thursday, I didn’t work, but a couple of my friends and I were like, wait, things seem to be heating up, should we maybe get like more food? Is this? It was a general sense of panic rising in the general populace and we were like, I don’t, I only have a couple of cans of something. So we actually went to Trader Joe’s and we’re shopping and it was totally empty, like absolutely zero products in the frozen section, like no bread, and that’s when I was like, oh, next time I have to come into work this is, this is going to be my reality. And that’s what sort of landed for real.
Alex Wagner: When did you feel like Trader Joe’s, the company started taking the virus seriously.
Tony: It was that next week I specifically remember one of our managers, or one of our mates we call them. He sat, we call them huddle. It’s like a little group where a mate sits down and goes over updates. This one was specifically pertaining to the coronavirus.
Alex Wagner: What was the general tenor of that that first meeting, if you could recall?
Tony: Yeah, it was it was definitely nowhere near like: you guys are going on the front lines, this is going to be crazy, get ready, get—it was much more like, hey guys, we know that this is a community store, we operate kind of like as a pillar of the community, we know people are going to come here and expect a good, like a normal shopping experience and so it kind of falls to us to be that pillar of the community. I remember specifically, like that notion being impressed upon me that the role that we have always fulfilled is not going to change. When people come in, they’re like, oh, thank God, Trader Joe’s, just as I remembered it, maybe they’re disinfecting the carts a little bit and maybe they’re making me put on hand sanitizer as I walk in the door, but it’s still Trader Joe’s, it’s still the friendly, smiling, helpful employees that I’ve always known. So that was when they first mentioned this, the notion of a two-week leave that we could take if we wanted. Specifically an unpaid two-weeks, no questions asked, you just take it. The difference from just otherwise taking a leave is that this one wouldn’t count against your benefits.
Alex Wagner: You guys are working. You’re interfacing with a lot of people, some of whom may be sick and they don’t even know they’re sick. And you’re in an environment and in a place that is the source of a lot of concern, if not downright panic. People want to get their food. They want to get out of there. Did they talk to you about how you should handle yourselves to make sure you guys were safe and could protect yourselves from the virus?
Tony: Yes. So at first, it wasn’t so much with regards to any personal protective equipment. I do remember in that first meeting, it wasn’t really, not that I remember that they were ever mentioning specifically the hazards that we would encounter—coughs, sneezes and other forms of contamination from customers—other than things that have been generally creeping into the public knowledge of, like, whether or not to wear masks, things like that. As that came out, they sort of addressed it, but specific to our grocery store environment, they weren’t very specific about what we should necessarily expect. And I think to their credit, a lot of that was because I don’t think anyone really knew what to expect and what it was going to look like as the days progressed. There was a little confusion as to whether or not we were allowed to wear gloves as we were working, like rubber gloves as opposed to like our normal work gloves. Some people are saying yes, some people were saying no. Ultimately, the decision was made clear that we could wear gloves if we were more comfortable with it, even though the CDC was not recommending gloves. But I think a lot of people were like, I would just want to wear gloves just for my own sense of cleanliness. But at first they were saying masks were not allowed and then, and then after that sort of set in, then we started to definitively allow gloves, could totally do that. We were sanitizing much more.
Alex Wagner: Do you remember when, like when this was this last week, was this two weeks ago?
Tony: The gloves phased in about two weeks ago. And then with, in this past week, we started really ramping up our sanitation game. And then last week was when we started doing, like the crew members were at the door allowing only certain numbers of people in to shop. So the line was forming outside. And we are, we started off keeping around 60 and we soon since brought it down to like 40, so that the total number is around 60, including our employees.
Alex Wagner: Just to be clear, that’s 40 people inside the store at any given time,
Tony: 40 customers, plus 20 to 30 crew members equaling 60 to 70, was the, that’s how the math is being laid out.
Alex Wagner: And as this is happening, as Trader Joe’s kind of goes from saying, you know, if you’re uncomfortable, let us know to, yes, you can wear gloves but don’t wear masks to, OK now we’re severely cutting back on the number of people who are even allowed in the store, as that concern starts ramping up and is evident in store policy, how are employees feeling, the people who have to work in these stores? Is there like any kind of alarm setting in or what would you describe the mood among crew members as?
Tony: A little it’s pretty dark in there, I’m not going to lie. Going to work is not as bright and cheery and enjoyable as it was even a few weeks ago. There’s palpable anxiety in the air, both from the customers, from the crew, like once they said we could wear masks, people are wearing masks immediately.
Alex Wagner: When did they say you could start wearing masks?
Tony: That was in the past couple days, I was in Sunday, and it was like no masks, and then today it was yes masks, so it was a pretty quick turnaround. And I think, again, there management is recognizing that we want these things, even if maybe it doesn’t actually help us at all, but it’s just to make us feel like we’re a little safer, it’s worth its own weight.
Alex Wagner: Do people feel like they’re going to get the virus eventually?
Tony: I have heard that. I have heard people just sort of talk about the inevitability of it. Speaking of that two-week leave that I mentioned earlier, we had a bunch of crew members who have been taking that in kind of every couple of days someone will post on their Facebook page, okay, guys, I’m taking my leave. Like, alright, another one bites of dust.
Alex Wagner: So it sounds like there is some sort of social networking inside the Trader Joe’s family. You guys have a Facebook group where you’re sort of sharing fears and anxieties, is that right?
Tony: Yeah, that’s absolutely. So there’s a couple different Facebook groups out there. There’s one that’s specific to our store, and that’s the more personal one. People we know each other and that’s one where people are expressing their two-weeks and saying that they’re taking off or expressing like, hey, guys, does anyone know if we are now allowed to use masks? People comment and respond. There’s also a larger one that’s nationwide and that’s a private group. It’s for just crew members. Theoretically, no management. But that’s kind of questionable at times. And it’s more of a, is any store have the face guards in? Apparently, some stores are now getting the Plexiglas shields on the registers. We’ll see if that happens at our store. And I think the first person that left on their leave that I know of is returning tomorrow. So they left two weeks ago. And it seems a little bit, a little bit odd because then if they were safe, theoretically safe those two weeks and then returning to a theoretically unsafe space, then that seems kind of to defeat the whole purpose. That kind of notion is setting in as well, that the while like we’re all sort of breathing the same tiny break room and—
Alex Wagner: So you guys are all still congregating in the same break room?
Tony: Yes, yeah. So there’s a sense that if one of us gets it, like we are all going to get it, probably.
Alex Wagner: How many people congregate in the break room on average?
Tony: Anywhere from two or three, up to six or eight if it’s like around break time, which is the middle of a shift. It could be even more depending on circumstances. I think people are generally trying to keep it low, even if we’re not recognizing it. Because we recognize that there’s not much air circulation going on in that room, it’s not the ideal place to be during a situation where you could easily take [unclear].
Alex Wagner: Has there been any talk about maybe screening people for fevers when they come in for a shift or any of those measures? Are they giving you guys gloves and masks and hand sanitizer at this point?
Tony: There’s been no mention of screening. I saw a headline about some other store that was screening customers as they came in, and I was like that seems like, I don’t think we would ever take that. That doesn’t seem like something that we as a store would do.
Alex Wagner: Why, why do you think that?
Tony: In everything I have experienced at Trader Joe’s, it’s about creating an atmosphere that is very conducive to like customer comfort. And usually it works out nicely that that also aligns with crew comforts and it doesn’t have to kind of, they don’t have to butt heads at all. And I think this is a case where those two things don’t necessarily coincide. Because things that we might have to do for our protection, might inconvenience customers. And that’s, I think, a place where the company, it’s a gray area, and they leave a lot of the discretion up to the captains of each individual store.
Alex Wagner: I think there are a lot of people who may or, may be familiar with Trader Joe’s because they’ve shopped there or know someone who shops there, and there is, it’s sort of a different kind of a grocery store, right? Because it is very much community oriented. You guys are known as crew members. There’s a sense that you’re all in it together. But you’re a person who’s reading the news. You’re a citizen of the United States of America. You’re a member of this democracy. You see what’s happening across the country and you see the extraordinary measures that state and federal governments are going to to keep people safe, which includes locking down 250 million Americans effectively in their homes. But you’re going to work every day, and it doesn’t sound like there are any real safeguards in place, and that it’s completely discretionary. And for the average person that’s listening to you describe that, I think a lot of people are going to be afraid for you, Tony.
Tony: Yes, those are all very valid points. I would say that at this point, with all the safeguards in place, because I know my mom and my roommate have both been pretty frequently checking: do you still feel safe going to work? You asked earlier are there providing gloves and masks. They are providing, they’re providing us with alcohol spray, alcohol wipes and this other spray that we use, that’s, you read the label and it kills every virus I’ve ever heard of under the sun.
Alex Wagner: Sure but the fact, right, the fact that you guys are still congregating—
Tony: Yes.
Alex Wagner: In numbers more than two in break rooms and it just doesn’t feel like as everyone’s kind of going through these pretty hard, instituting pretty hardcore measures, it sounds like this environment is still a few weeks behind where we are, even at the federal level. Is that unfair to say or I mean, I don’t know. I don’t work there. You do. But just from what you’re telling me.
Tony: I think that that is very fair. I think that the mindset that I’m in when I’m home and I’m trying to avoid everyone who doesn’t live in my house and I’m being totally socially isolated, I get my car drive to work and I get out of the car and I’m like, OK, I shed that layer of precaution. That is true. I do, I can say that I have noticed that I get there and I put on a whole new set of precautions, but the same sense of social precautions might be, they king of fade a bit. Because we are a store with, even if we only have 40 customers, I’m walking around, like as I’m stocking product customers are just like reaching across me and part of me is like, are you guys not noticing, you’re not notice me here? OK, guys, that’s six-foot rule applies even if I’m just here stocking your groceries, for myself and yourself. I think that if you were to take someone who knows what they’re talking about as far as social distancing and all the precautions we should be taking and just give them a little a snapshot, like a video of what we do at the store, they might be a little concerned. I, I think it’s fair to say.
Alex Wagner: It’s pretty clear that you guys are taking on extra risk. I’m not sure if you’re taking on extra hours, but are you being compensated differently during the pandemic?
Tony: So our normal hourly pay has not changed. There’s no additional quote “hazard pay” that some of the stores are having. What we have is, there was a certain time period in which our hours worked are factored in with our store sales. It’s some complicated algorithm that, or something that is kind of confusing to date. And then basically output is, and it was just kind of like a bonus that everyone got.
Alex Wagner: And can you give us a sense of the size of those bonuses?
Tony: Smaller than I think most people were anticipating? I know there’s a lot of discussion in the store and on the Facebook page about like, really!? it was a little bit less than we think we might have deserved being that we are actively exposing ourselves to a much higher risk. The number that they said, to answer all these questions that we were also having, was it’s going to come out to be at least like a $2 more per hour. A lot of the, a lot of the news comes down in whispers, he said she said kind of situation, so I haven’t confirmed that. I’m going to look into that because that would be a lot nicer because I have been picking up a lot more hours lately, so.
Alex Wagner: Well, you’re also picking up a lot more risk.
Tony: Yes, exactly.
Alex Wagner: You’re also picking up a lot more risk. I wonder, given the circumstances under which you guys are working and the remuneration that’s happening where, I mean, were people angry about that?
Tony: There was a decent spectrum of reaction. A lot of people are like, hey, it’s money, well, I’ve never been mad to get money. And other people are like, are you kidding me, this is ridiculous. And everything in-between. People are mad. People are like, well, at least it’s better than nothing. I don’t really know where I fly. A little mix of each of those, to be honest. But I do get the sense that there are some, there are some pretty pissed people out there, and I don’t really blame them, to be honest.
Alex Wagner: Do you ever wonder how it is that you ended up on the front lines of a global pandemic? I mean, do you ever question whether you should go to work tomorrow? I know that there’s an economic imperative in all of this, but some people would say, oh, man, the risk is just not worth it. Is that ever a calculation you make or that you think other people in the store are making?
Tony: Yes, other people definitely are, because people are taking that leave of absence and are just, and a lot of people when they have been posting on Facebook page, and they may give a little spiel like I’m doing this because I live with my immuno-compromised partner, or with my grandma, I don’t want her to be at extra risk. So I think a lot of people are making the calculation, then like being out there is not really worth, not really worth the risk that I’m facing. I thought about this a lot. My roommate is asthmatic, so I’ve been very careful to, when I do work, I get home, I pretty quickly just throw everything in the dirty clothes bin and take a very hot shower and wash everything. I’ve been wiping down our groceries now when I bring them in. I’m trying to be very careful there. And if, honestly, if, and I think I think honestly, that terrible, terrible youthful sense of invincibility that we’re seeing on, around everyone, I think, I’m I think I’m a victim of that. Where I think, I’m still young and healthy, like nah, I’m good. And then it’s like you can still, look at the data, like the data demonstrating that you are absolutely susceptible to not only getting this disease, but being hospitalized. It’s a very distinct possibility that I could get this virus and it could lead to a really, really bad outcome. So at times like that, I like to just sort it eat some Trader Joe’s snacks wait till tomorrow to make a decision about that.
Alex Wagner: Thanks, Tony. It’s so great that you were able to talk to us, man. Super appreciate it. And it’s really wonderful to have perspective on what you guys are all going through. Needless to say, we are all so thankful for what you’re doing to keep us fed. You know, we’d be lost without you.
Tony: Doing what we can. We were keeping that Trader Joe’s spirit as high as we can. Holding the flag high.
Alex Wagner: BuzzFeed is reporting that the bonus Tony was referring to was announced after workers started a petition which to date has been signed by over 20,000 people, calling on Trader Joe’s to give its employees hazard pay at the rate of time and a half.
Alex Wagner: That’s all for this episode of Six Feet Apart. Our show is produced by Alisa Gutierrez and Lyra Smith. Lyra Smith is our story editor. Our executive producer is Sara Geismer. Special thanks to Alison Falzetta, Stephen Hoffman and Sidney Rapp. Thanks for listening. And stay safe.